Как интегрировать WMS с принципами HACCP на складе
Эксперт по автоматизации, генеральный директор «Технологии учета» рассказал как WMS улучшает прослеживаемость товаров и осуществляет контроль на складе
Генеральный директор ООО «Технологии учета», основатель компании, совмещающий в себе стратегическое мышление с техническими компетенциями и отличными лидерскими качествами.
В современных реалиях безопасность и качество товаров являются первостепенными, не только производители пищевой промышленности, но и все предприятия в пищевой цепи (распределительные центры в части хранения и комплектации, складская и транспортная логистика в части доставки и т.п.) сталкиваются с растущими требованиями к соблюдению условий по прослеживаемости грузов. Для успешного выполнения этих требований все больше компаний интегрируют систему управления складом (Warehouse Management System, далее — WMS) с принципами HACCP/ХАССП (Hazard Analysis and Critical Control Points — Анализ опасностей и критические контрольные точки). В этой статье поговорим о том, как интеграция помогает в управлении рисками, улучшении процессов контроля качества и безопасности и минимизирует возникновение серьезных несоответствий в складской логистике.
К каким сферам в складской логистике применимы принципы HACCP
Использование в работе контрольных точек для управления заказами и внедрение прозрачной системы прослеживаемости товаров крайне важны для склада в любой сфере, потому что принципы, которые использует система управления рисками для улучшения деятельности применимы к компаниям, находящимся по всей цепи создания пищевой продукции. На первый взгляд, они могут быть далеки от «классических пищевиков». К ним могут относиться производители пестицидов, удобрений, ветеринарных препаратов, оборудования и упаковки, веществ и материалов, чистящих и санитарных средств, сервисные, транспортные, логистические компании, интернет магазины с собственными складами хранения и т.п.
Как пример — инструменты бережливого производства зародились и применялись изначально только в автомобильной промышленности, а сейчас используются в разных сферах, в том числе и в складской логистике, потому что позволяют стандартизировать деятельность и управлять потерями системно.
Основной фундамент методологии ХАССП — выделенные опасные факторы, или факторы, имеющие прямо или косвенно отношение к рискам, которые могут возникнуть или обязательно возникнут в процессе всего жизненного цикла продукции, и тогда продукция не сможет считаться безопасной для конечного потребителя. То есть, все компании, которые попадают в цепочку доставки продукта от производителя до клиента должны их учитывать, и складская логистика часто сталкивается с необходимостью применять следующие принципы в работе:
- Анализ и идентификация потенциальных опасностей товаров на всех стадиях (приемка, хранение, перемещение, комплектация, отгрузка).
- Определение критических контрольных точек (далее — ККТ) или этапов, на которых необходимо осуществлять контроль и фиксировать данные. Это все измеримые показатели, например, температура, влажность, вес, время, которые значимы для определенной категории товаров (опасные грузы, пищевые, косметические товары, детское питание, лекарственные препараты).
- Установление пределов для ККТ: определение приемлемых значений параметров для измеримых показателей.
- Мониторинг ККТ.
- Корректирующие действия в случае возникновения несоответствий.
- Верификация или проверка эффективности реализации принципов.
- Документирование данных в процессе выполнения деятельности.
Например, в случае с распределительными центрами продуктов питания (далее — РЦ), которые сейчас показывают динамику роста бизнеса в сфере складской логистики, неизбежно происходит столкновение с аудитами сетей и ритейла, потому что они отслеживают выполнение требований на всех стадиях и все перечисленные принципы должны выполняться в полной мере.
Примеры применения принципов оценки рисков в складской логистике:
- хранение скоропортящихся продуктов: Для таких товаров, как молочные продукты, фрукты и овощи, критически важны условия хранения (температура, влажность), оценка опасных факторов помогает определить оптимальные параметры хранения и контролировать их соблюдение.
- логистика фармацевтических препаратов: Лекарства требуют соблюдения строгого температурного режима и защиты от загрязнения, соблюдение принципов позволяет разработать систему хранения и транспортировки, которая гарантирует сохранность качества лекарств.
- хранение опасных грузов: Вещества, классифицируемые как опасные (токсичные, взрывоопасные, легковоспламеняющиеся), требуют особого внимания. Оценка рисков помогает определить меры по безопасному хранению и транспортировке таких грузов, минимизируя риски возникновения пожаров и других аварийных ситуаций на складе.
- контроль санитарно-гигиенических условий склада: Чистота склада, дезинфекция оборудования и борьба с вредителями — важные аспекты содержания склада, регулярный контроль и соблюдение санитарных норм предотвращают загрязнение товаров.
Применение принципов ХАССП помогает выявить слабые места в системе менеджмента склада и внедрить более эффективные процедуры, является не просто формальностью, а необходимым условием для обеспечения безопасности товаров и повышения эффективности логистической деятельности.
Основные преимущества внедрения оценки рисков в складской логистике:
Повышение качества продукции: Обеспечение надлежащих условий хранения и транспортировки товаров минимизирует риск их порчи, повреждения или снижения качества во время нахождения на складе.
Сокращение потерь: Выявление и устранение потенциальных рисков, связанных с хранением и транспортировкой, позволяет минимизировать потери товара от порчи, кражи или других причин, сказывающихся на рентабельности бизнеса.
Улучшение безопасности: Контрольные точки помогают предотвратить несчастные случаи и травмы на складе среди персонала, оптимизируя процессы работы и обеспечивая тотальную безопасность и сотрудников и заказов.
Повышение эффективности: Оптимизация процессов хранения и транспортировки, а также минимизация потерь, повышают эффективность складской логистики и сокращают затраты.
Улучшение репутации: Обеспечение высокого качества продукции и услуг, а также соблюдение всех стандартов безопасности укрепляет репутацию компании на рынке и повышает ее конкурентоспособность.
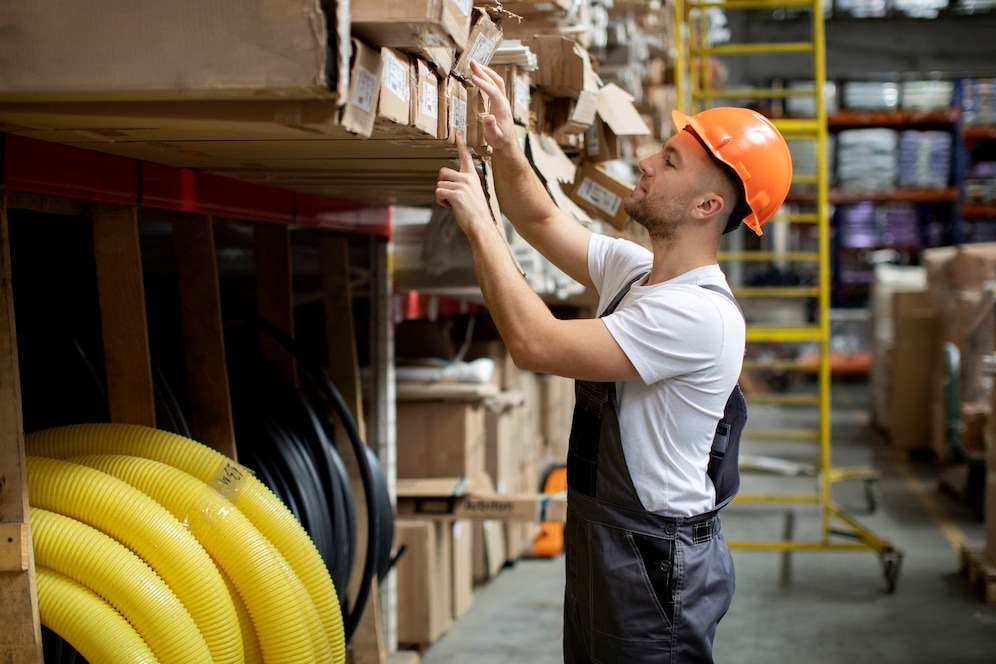
Как интегрируются WMS и принципы ХАССП
Система управления складом (WMS) представляет собой программное обеспечение, предназначенное для оптимизации всех процессов, связанных с хранением, перемещением и отгрузкой товаров на складе и позволяет компаниям:
- автоматизировать процессы приема, хранения и отгрузки, минимизируя ошибки и повышая эффективность операций технологических процессов;
- оптимизировать использование складских площадей за счет повышения пропускной способности склада, что приводит к снижению затрат и повышению производительности;
- обеспечить точный контроль запасов в реальном времени, предотвращая перепроизводство и дефицит.
ХАССП фокусируется на предотвращении проблем с безопасностью, а не на их устранении после возникновения, поэтому интеграция с WMS позволяет значительно повысить безопасность товаров во время хранения. Автоматизированная система управления складом обеспечивает точное отслеживание всех этапов движения продукта, что позволяет контролировать условия хранения и быстро идентифицировать источники проблемы в случае возникновения инцидента — ошибки персонала, нарушение правил безопасности, не соблюдение условий и прочее.
Система прослеживаемости использует RFID-метки, штрих-коды и другие технологии идентификации для сбора данных о местонахождении и статусе товара. Например, AS WMS может быть интегрирована с датчиками и системами мониторинга, которые автоматически отслеживают параметры ККТ, такие как температура, влажность и срок годности товаров.
Мониторинг и аналитика данных движения товаров в режиме реального времени дает полное представление о состоянии запасов и местонахождении каждого товара, можно обнаружить проблемы на ранних стадиях, а точная информация о статусе заказа и сроках доставки повышает уровень доверия к компании.
Улучшенное управление рисками — благодаря системе помогает определить критические контрольные точки (ККТ) на складе, это этапы в процессе обработки грузов, на которых необходимо обеспечить строгий контроль для поддержания качества и безопасности.
ККТ в складской логистике могут включать в себя:
на этапе «приемка товаров»: проверка соответствия поступающей продукции спецификации, заявленному количеству и полноты комплектации.
на этапе «хранение товаров»: контроль условий хранения (температура, влажность), расположения товаров на складе, соблюдение сроков годности, принципов FIFO и FEFO.
на этапе «комплектация заказов»: контроль точности сборки заказанных товаров в соответствии с требованиями клиента.
на этапе «отгрузка»: проверка полноты комплекта и состояния отгружаемых товаров, соответствия упаковки и маркировки.
Сокращение потерь — WMS помогает оптимизировать условия хранения продуктов, предотвращая порчу и убытки. Оптимизация процессов на контрольных точках ведет к сокращению простоев, уменьшению количества брака и снижению трудозатрат. Строгий контроль качества и прозрачность процессов, обеспечиваемые интегрированной системой, повышают доверие.
Примеры использования WMS для управления контрольными точками: система может отслеживать сроки годности лекарств, контролировать условия хранения и генерировать отчеты о потенциальных рисках в фармацевтической компании; управлять контролем качества сырья, соблюдением санитарных норм при хранении и отгрузке продукции на пищевых производствах.
Основные этапы интеграции:
- Анализ рисков: Идентификация всех потенциальных рисков, которые могут возникнуть на складе, связанных с хранением, транспортировкой и обработкой товаров. Операции процессов разбиваются на стадии, например «приемка», «хранение», «отгрузка», «отбор проб», «возврат товара».
- Определение контрольных точек и ключевых этапов в процессах складской логистики, где необходимо контролировать риски. Например, на стадии «приемка» это могут быть риски поступления товаров с неполной комплектацией, с браком или несоответствиями по маркировке.
- Определение допустимых параметров и разработка процедур контроля, включающих в себя методы мониторинга, измерения и внесения корректировок.
- Создание системы документации, включая результаты мониторинга, корректирующие действия и другую информацию.
- Проведение обучения персонала процедурам контроля и ведения документации.
- Регулярный анализ аналитики и внесение необходимых изменений и совершенствование системы.
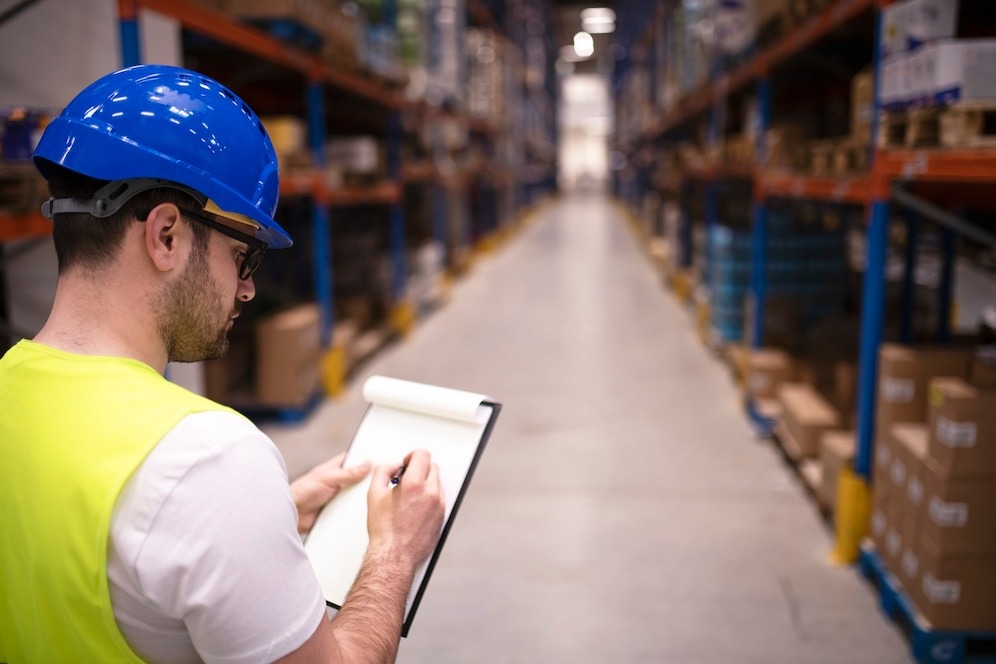
Примеры автоматизации контрольных точек с помощью WMS
Применение WMS для управления контрольными точками требует комплексного подхода, включающего в себя не только установку программного обеспечения, но и закупку специального оборудования (датчики, системы автоматизации), наличие квалифицированного персонала. Необходимо учитывать специфику поступающего товара на склад, условия хранения и требования нормативных документов при автоматизации. Регулярное обслуживание и калибровка оборудования, а также обучение сотрудников работе с WMS являются важными факторами для эффективного управления контрольными точками. Далее приведу несколько примеров:
1. Приемка товара:
- Сканирование штрих-кодов: WMS интегрируется со сканерами, автоматически регистрируя поступающий товар и сверяя его с заказом. Это минимизирует риск ошибок при ручном вводе данных и ускоряет процесс приемки.
- Контроль качества: WMS может быть настроен для автоматического запуска проверок качества товара на соответствие стандартам.
- Фотографирование и идентификация: Системы с функцией распознавания изображений позволяют автоматически идентифицировать товар по его визуальным характеристикам, что повышает точность и скорость обработки.
2. Хранение товара:
- Оптимизация размещения: WMS анализирует характеристики товара (размер, вес, частота отгрузки) и доступные складские площади, автоматически предлагая оптимальные места для хранения.
- Управление запасами в реальном времени: Постоянный мониторинг уровня запасов позволяет избежать дефицита или переизбытка товара, оптимизируя закупочные процессы.
3. Сборка заказов:
- Генерация маршрутов сборки: WMS генерирует оптимальные маршруты для сборщиков, минимизируя время и расстояние прохождения.
- Подтверждение сбора по сканеру: Сканирование штрих-кодов на каждом этапе сборки гарантирует точность и предотвращает ошибки.
4. Отгрузка товара:
- Проверка отгрузки: WMS сверяет собранный заказ со списком, выданным на отгрузку, и генерирует сопроводительные документы.
- Отслеживание доставки: Интеграция с системами GPS позволяет отслеживать местонахождение груза в режиме реального времени.
5. Анализ данных:
- Выявление узких мест: Анализ данных позволяет выявить операции, которые замедляют весь процесс, и принять меры по их оптимизации.
- Оптимизация использования ресурсов: WMS помогает эффективно распределять персонал и оборудование, минимизируя простои и повышая производительность.
6. Управление температурой и влажностью
К примеру, компании необходимо обеспечить хранение продуктов питания, лекарств или других товаров, требующих строгого температурного режима. WMS может получать данные с датчиков температуры, установленных в холодильных камерах, складах и на транспортных средствах. При выявлении несоответствия (выходе температуры за установленные пределы), система сохраняет данные мониторинга за определенный период, что позволяет анализировать условия хранения и выявлять потенциальные проблемы на будущее. Например, если температура в холодильной камере для вакцин превышает определенный предел, будет отправлено уведомление и автоматически блокироваться доступ к товарам, пока температура не нормализуется или не будут приняты меры. То же касается влажности — если компании необходимо обеспечить хранение товаров, чувствительных к влажности (такие сферы как электроника, бумага, текстиль), WMS получает данные с датчиков влажности, установленных в складах и вести аналитику в режиме реального времени для принятия своевременных решений.
В заключении отмечу, что внедрение WMS с точками контроля является стратегическим решением для компаний, стремящихся к повышению эффективности, безопасности и качества логистических операций, а также задумываются об устойчивом развитии.