Как с помощью бережливого производства повысить производительность на 56%
Производитель электротехнического оборудования Электрощит Самара совместно с РЦК Самарской области улучшил процессы и увеличил выпуск продукции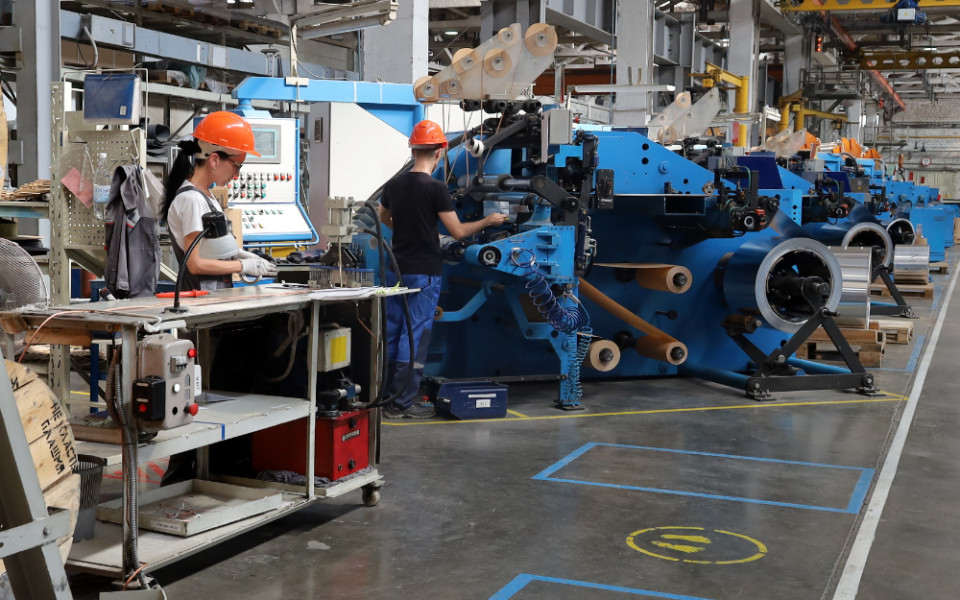
Задача:
Повышение производительности труда на пилотном потоке «Оптимизация процесса изготовления трансформатора масляного типа ТМГ-250/400/630».
Причина:
Потеря прибыли из-за упущенной выгоды; Низкое соответствие фактической производительности к максимально расчетной производительности на сварке; Пересечение потоков, не сбалансированная работа участков.
Электрощит Самара является высокотехнологичной производственной компанией и крупнейшим российским производителем электротехнического оборудования в сегменте 0,4–220 кВ. Предприятие более 80 лет активно развивает родное отечественное конкурентоспособное оборудование, строит новые подстанции, увеличивает мощности и обеспечивает надежность энергосистемы страны.
Несмотря на уже имеющийся опыт в бережливом производстве, руководство компании приняло решение оптимизировать производственные процессы, в рамках национального проекта «Производительность труда». Внедрение инструментов бережливого производства проходило на базе производственной площадки «Русский трансформатор».
Эксперты РЦК провели картирование потока создания ценности в производстве трансформатора масляного типа на примере ТМГ-1000 и выявили проблемные зоны с последующим проведением мероприятий по их устранению.
На участке оформления и приемки трансформаторов, к примеру, выявились следующие проблемы:
- ожидание комплектующих, поддонов и упаковки;
- оператор тратил время на поиск стандартных деталей;
- отсутствовала организация поста по 5 С.
В результате стали осуществлять процесс комплектации рядом с участком упаковки. А также организовали 2 Bin для стандартных деталей. Данные меры позволили увеличить выработку на посту оформления трансформаторов на 135%.Проблемным, узким местом, где все работает слишком медленно из-за наличия многозадачности и потерь, был и участок болчения крышки трансформатора.
Тормозили производственные процессы на участке такие причины:
- на посту работал только один оператор;
- бак периодически находился за пределами места расположения пневмогайковерта, поэтому оператор затягивал гайки гаечным ключами;
- оператору приходилось ждать кран-балку для перемещения бака.
Улучшить производственные процессы удалось с помощью организации дополнительной точки с сжатым воздухом, исключения перемещения трансформаторов за счет удлинения пневмошлангов для гайковертов и дооснастки поста пневмоинструментом. Что в итоге повысило выработку на посте болчения крышки на 224%.Были выявлены проблемы и на участке заливки под вакуумом:
- скопление трансформаторов перед заливочной машиной;
- поломка второй заливочной машины;
- пересечение потоков, использующих кран-балку.
Увеличить выработку на участке заливки вакуумом на 51% удалось с помощью ремонта второго оборудования для заливки, формулировки правил и критериев задействования второй заливочной машины.
Узким местом был и участок сушки магнитопровода. Здесь выявлены следующие проблемы:
- участок шихтовки ожидал магнитопровод;
- скопление большого количества собранных магнитопроводов перед сушкой;
- малый размер партии устанавливался на поддоны в печь.
С помощью увеличения количества магнитопровода на поддонах и организации сушки в ночную смену выработка на участке возросла на 68%
На эталонном участке сварки, зачистки и проверки на герметичность баков и крышек ТМГ с помощью методик бережливого производства также решены ряд проблем:
- пересечение производственных и логистических потоков;
- посты не соответствовали требованиям ОТ и эргономики;
- баки комплектовались самим сварщиком.
Решением стали реорганизация участка под производство по одному изделию, организация трех параллельных линий сварки и комплектование постов, перебалансировка операций сварки и выделение в отдельное производство сварки крышек и доньев.
На участке сварки было 3 поста сборки и 6 постов обварки баков. Комплектующие поступали на посты сборки баков. Так как время цикла обварки было больше времени сборки, собранные баки вывозились с участка на временные места хранения. Затем их вновь завозили на посты обварки. И только после этого — на место хранения для поверки ОТК. А позднее — в другой пролет для зачистки и поверки на герметичность.
Лишние перемещения и движения при поиске необходимых баков и комплектующих к ним выливалось в большое количество НЗП между операциями сборки и обварки. Что, в конечном итоге, приводило к неритмичному выходу готовых корпусов трансформаторов и срывам сроков поставки.
Проведенные хронометраж операций и их анализ. На их основании проведена перебалансировка операций между рабочими местами, что позволило организовать процесс сварки баков в виде трех поточных линий из 3 постов с тактом в 60 минут. Для чего переместили сварочные посты согласно планировке в 3 поточные линии и организовали зону комплектации внутри сварочного участка. Так же переместили участок зачистки с дальнего пролета ближе к участку сварки.
Все вышеизложенные меры на участке сварки баков позволили повысить выработку на 51%.
Были проблемы и на участке комплектации. Так хранение деталей и подузлов осуществлялось без адресного хранения на территории заготовительного участка в рабочей зоне. А комплектование производилось «со станка» сварщиками под сменное задание.
Решением проблем стала организация стеллажного хранения с обеспечением идентификации деталей. Стеллажи размещены в непосредственной близости к сварочному участку. И хранение из производится по частоте использования и габаритам (ABC-FMR анализ).
Руководитель проекта РЦК Илья Арискин:
«Благодаря эффективным мероприятиям по бережливому производству и активному участию рабочей группы предприятия удалось значительно сократить время процесса, увеличить производительность и выработку продукции».
Генеральный директор Электрощит Самара, Дмитрий Куприянов:
«В апреле 2023 года Электрощит Самара вошел в число участников национального проекта «Производительность труда», инициированного Президентом РФ. Обозначенные задачи в рамках нацпроекта — повышение конкурентоспособности российских товаров и услуг, создание культуры высокой производительности и эффективности — полностью согласуются с текущими целями нашей компании. Участие в нацпроекте позволило нашему предприятию провести целенаправленное улучшение производственных мощностей. Внедрение методик бережливого производства в компанию было осуществлено совместно с Региональным центром компетенций в сфере производительности труда (РЦК). Благодарим РЦК за доверие, поддержку и содействие в процессе усовершенствования производственных мощностей».
Увеличение -выработки на чел.-час на 55%; -производительности на 56%; -выработки продукции в месяц на 37%. Снижение -времени протекания процесса на 52,3%; -незавершенного производства на 14%.
Интересное:
Новости отрасли:
Все новости:
Публикация компании
Достижения
Профиль
Контакты