Как достичь стабильности в экономических показателях ТОиР
Личным опытом поделился Денис Труфакин, директора Центра экспертизы ТОиР Деснола, разработчика и интегратора экосистемы 1С:ТОИР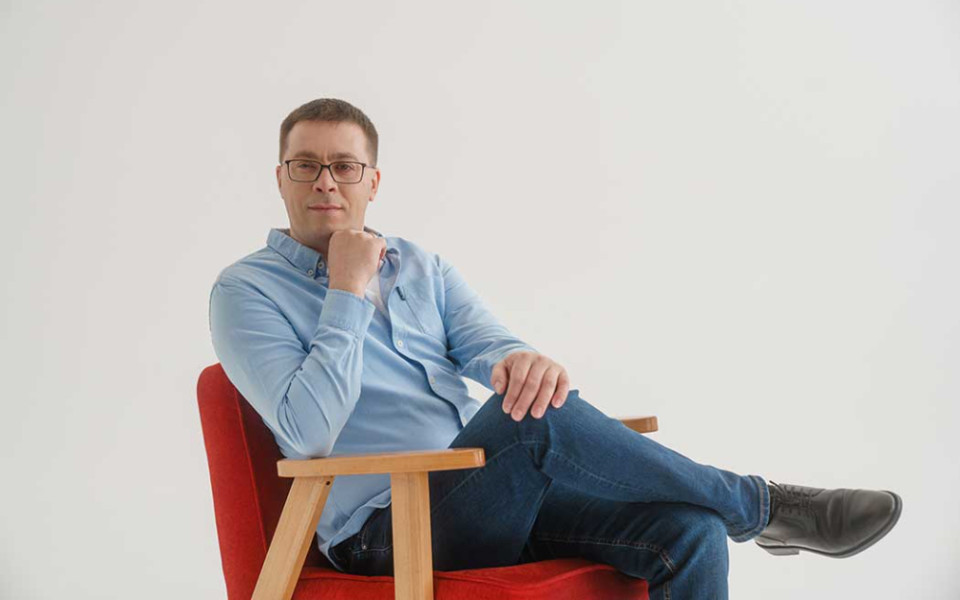

Куратор и участник проектов цифровизации ТОиР на десяти производственных площадках России в роли главного инженера и руководителя технического управления
Четыре области оптимизации
Денис, как Вы пришли к стабильным экономическим показателям в ТОиР?
Везде, где есть оборудование, нужно управлять активами. Вопрос: как? Чтобы получить эффект или достичь измеримой цели, необходимы данные. Расскажу о личном опыте. Когда мы запускали проект автоматизации процессов управления ТОиР на одном из крупных отечественных предприятий — 7 производственных площадок по стране и свыше 15 элеваторов — мы начинали с пяти основных структурных организаций. Учет простоев там велся только тогда, когда не выполнялся производственный план. Как только сталкивались с невыполнением, начинали разбираться в причинах отказов. Очевидно, что необходимо было наладить регулярный сбор данных и организовать ведение статистики о состоянии оборудования и дефектах, чтобы понимать реальную картину неисправностей.
С каких данных начинали?
С точки зрения управления активами можно выделить четыре области оптимизации, в которых, с одной стороны, есть основные риски, с другой стороны, есть и основные эффекты. Это повышение общей эффективности оборудования (Overall Equipment Effectiveness или OEE), сокращение затрат на ремонт оборудования, снижение оборотного капитала, оптимизация оргструктуры и трудозатрат.
Каждая компания, как правило, ставит для себя цели, ориентируясь на показатели одной из этих четырех областей. Например, для белорусской ГК «Алютех» было важно решить с помощью EAM-решения «1С:ТОИР Управление ремонтами и обслуживанием оборудования КОРП» проблему с оптимизацией складских запасов. В связи с задержкой в поставках запасных частей — иногда до года — запасы производителя алюминиевых профильных систем выросли в 1,5 раза, а это в том числе дорогостоящее оборудование стоимостью €100 тыс. за единицу. Компания завершила совместный с Деснолом проект в декабре 2023 г. и теперь до конца 2024 г. работает над нормализацией номенклатуры.
Экономический эффект в процентном выражении еще только предстоит оценить, но руководство уже может видеть разницу межу минимально необходимыми запасами запчастей и реальной картиной на складе: завышено ли количество складских запасов или, наоборот, их не хватает, чтобы обеспечить минимальный уровень для поддержания бесперебойной работы оборудования. В практике Деснола есть примеры, когда материальные запасы в результате проекта автоматизации процессов управления активами сокращались на 5, 31 и 40 %.
Цель — улучшение OEE
А какие цели ставили вы на проекте?
На проекте, который я описывал ранее, мы ставили цель повысить общую эффективность оборудования через коэффициент технической готовности (КТГ). Для начала организовали учет простоев и стали считать общую эффективность оборудования объемным методом. Он позволил определить наличие простоев оборудования через разницу между планируемым и фактическим выпуском продукции. На закрытии смены объемный метод мог показать, что оборудование загружено, условно, на 650 минут, а простоев внесено на 20 минут. Суммарно получаем 670 минут, в то время как в смене — 720 минут. Где оставшиеся 50 минут?
Встреча этих двух направлений показала серую зону неклассифицированных простоев. Шаг за шагом мы начали их разбирать, классифицировать, и это дало первый эффект. Когда вышли на определенное плато, то с помощью монитора показателей KPI, специального отчета в системе 1С:ТОИР КОРП, начали контролировать среднюю наработку на отказ по повторяющимся простоям и среднее время ремонта. Нашли способ сокращения ремонтов по тем отказам, предупреждение которых было слишком дорогостоящим мероприятием.
Поднакопив определенное количество данных, провели приоритизацию оборудования по внеплановым ремонтам. Получив здесь эффект, снова увидели потенциал и возможности для развития. С помощью 1С:ТОИР КОРП и отчетов мы могли уже показать акционерам потенциал в деньгах. Так, каждая потеря времени в отчете пересчитывалась в недовыпущенный объем продукции.
Мы могли также показать в сравнении затраты на аварийный ремонт по сравнению с плановым. Это помогало развивать проект, так как мы оперировали обоснованной информацией, зачем нам дополнительное финансирование и к чему приведет закупка диагностического оборудования и специализированного программного обеспечения, введение новой должности — диагноста, и обучение сотрудников работе с программными продуктами.
Фокус на качество исходных данных
Как ввод должности диагноста помог развитию проекта автоматизации ТОиР?
Диагносты на основе данных системы мониторинга помогли определить проблемы на более ранних стадиях возникновения неисправностей в работе критичных активов. Мы смогли увидеть, что специалист обращается к одной единице оборудования каждые три недели. А P-F интервал, или время между потенциально возможными (P) и реальными функциональными отказами (F), например, подшипников сепаратора, может измеряться двумя неделями.
Разница в одну неделю показала, что в этот период времени оборудование может успеть сломаться, при этом отчеты по диагностике будут показывать, что оборудование исправно, так как при первой диагностике дефекта еще нет, а при второй диагностике дефект уже фиксируется как устраненный. Определили этот момент, установили стационарную диагностику, связали специализированное ПО с 1С:ТОИР КОРП и каждые пять минут стали получать актуальные данные о состоянии оборудования.
И что потом?
На основе этих данных провели анализ, который дал представление, что, например, где-то необходимо запланировать аварийный запас, где-то скорректировать список регулярно-потребляемых материалов, где-то чаще проводить осмотры и планово-предупредительные ремонты. Кроме этого, мы интегрировали 1С:ТОИР КОРП с АСУ ТП и начали в режиме реального времени получать информацию о наработке. Это помогло повысить чистоту данных и высвободить ресурсы мастеров на более важные, чем фиксация наработки ручным методом, задачи, например, на поиск корневых причин отказов. Также стали использовать мобильное приложение, которое позволило сократить трудозатраты в подразделениях при переходе на формирование нарядов в приложении на 16%, на 20% ускорить обработку заявок на ремонты.
Круговорот всех данных, заложенных в такую экосистему, приводит к тому, что управление активами становится более осмысленным, не содержится в головах отдельных сотрудников. Данные передаются не от человека к человеку по сарафанному радио. Здесь каждая функция распределена так, что одни сотрудники заносят данные (мастер), другие — анализируют эти данные и формируют конкретную программу обслуживания (инженеры по надежности), третьи (инженеры по планированию) — планируют программу обслуживания и выдают задания линейному персоналу.
Чтобы расти и постоянно повышать эффективность для бизнеса, мы собирали данные многоуровнево. Каждый уровень открывал новый слой данных и показывал свои определенные эффекты. Сначала мы получали укрупненные верхнеуровневые показатели. Затем стали прорабатывать глубину и чистоту данных. Постоянно увеличивая качество и количество данных, мы добивались конкретных результатов для бизнеса. И только, условно, на четвертом уровне уже получили КТГ близкий к 96 %.
Главное — это люди
Все эти шаги и стали причиной успеха в достижении экономического эффекта?
Не только. Важно, что мы сформировали команду и правильно выстроили коммуникации. Организационной готовности не было ни у кого, чтобы сразу прийти на четвертый уровень. Первое, с кого мы начали — это люди. Трансформировали структуру технической службы, которая классически состояла из отделов главного механика, главного энергетика и главного метролога.
В такой структуре каждый специалист отвечал только за свое направление. Не было единого центра управления процессами ТОиР. Мы переориентировали данную структуру на надежность: ввели в штатное расписание начальников ТОиР, диагностов, инженеров по надежности и планированию. Отдельное внимание уделили мотивации и обучению персонала работе в 1С:ТОИР КОРП и качественному внесению данных.
В конце концов, мы пришли к тому, что стали получать актуальную информацию обо всех активах в режиме реального времени. Рабочий день каждого участника проекта начинался с работы в системе. Исходя из данных EAM-решения мы планировали и корректировали свой рабочий день.
Конечно, были такие мероприятия, как входной контроль запчастей для критичных активов. Когда мы установили стенды входного контроля, то увидели до 80 % брака в подшипниках по отдельным поставщикам и брендам. Уровень шума был запредельным. Пришлось пересматривать абсолютно все складские запасы. Все это в комплексе привело к конечному результату и экономическому эффекту, но любой из пробелов в системе координат «люди — процессы — технологии» может привести не только к откату назад, но и к вопросу перевнедрения.
Как этого избежать?
Чтобы таких вопросов не возникало, необходимо еще до старта проекта автоматизации сформировать стратегию проекта цифровизации или цифровой трансформации процессов управления ТОИР, чтобы у всех было единое видение происходящих изменений и целей, к которым необходимо прийти. Чтобы у всех было единое понимание результатов происходящих изменений, и как эти результаты помогут каждому участнику процесса в его деятельности. Ну и, конечно, важен фундамент данных, который будет заложен в EAM-систему, так как это ваша будущая аналитика. И именно она даст понять, достигли ли вы целей бизнеса или нет.
Источник изображений: пресс-служба Деснола
Интересное:
Новости отрасли:
Все новости:
Публикация компании
Профиль
Контакты
Социальные сети