Без сбоя: автоматизированный склад сегодня и завтра
Без сбоя и без западных вендоров. Поговорим о том, какие превентивные меры стоит предпринять, чтобы обеспечить стабильную работу оборудования склада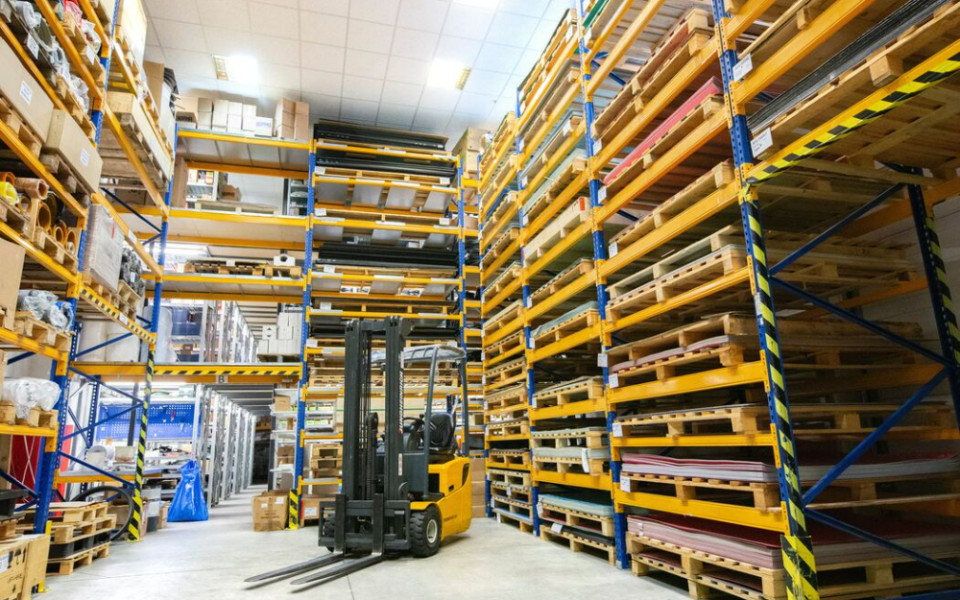
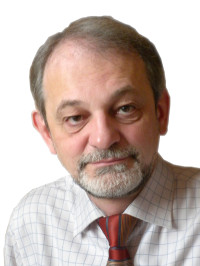
Эксперт-практик в области предпроектного консалтинга, бизнес-анализа, оптимизации складских бизнес процессов, предпроектной аналитике по выбору системы управления складом, разработке моделей и внедрении систем управления складом (WMS), интеграции складского оборудования с различными складскими системами, интеграция с производственными системами. Руководитель направления складской автоматизации в ИТ- компании, бизнес- консультант, педагог Московской школы бизнеса. Более 25 лет стажа в отрасли.
Современные технологии позволяют максимально автоматизировать и оптимизировать складские операции. Автоматизация задач управления складом осуществляется при помощи комплекса ПО, сердцем которого является система управления складом (WMS), которая работает в тесной связи с другими складскими информационными системами и оборудованием.
Уход западных вендоров с рынка для многих компаний породил сложности, с которыми до этого сталкиваться не приходилось: ремонт, покупка запчастей или замена оборудования стали крайне затруднены. Поговорим о том, какие превентивные меры стоит предпринять в такой ситуации, чтобы обеспечить стабильную работу оборудования.
Предиктивное обслуживание
Компании часто недооценивают важность контрольных визитов специалистов службы поддержки, так как не понимают сложность задач. Цель таких визитов не только в том, чтобы проверить состояние оборудования, но и обратить внимание клиента на некоторые проблемы, которые для него могут быть неочевидны.
Предиктивный анализ становится необходимым инструментом для российских компаний. С помощью этого метода можно обнаружить определенные отклонения, сигнализирующие о неполадках еще задолго до возникновения самой проблемы (небольшие скачки напряжения, повышенная вибрация, задержка при запуске двигателя, непонятный шум, минимальные изменения углов конструкций и т.п.). Источником данных о наличии таких неполадок в первую очередь служат системы визуального контроля, которые получают информацию камер, датчиков и т.п., анализируют полученные параметры и сравнивают их с нормативами. В случае отклонения от показателей система передает данные о необходимости принятия определенных мер и технического обслуживания. Второй по важности источник данных — это опыт работы сотрудников с конкретным оборудованием.
Причины сбоев
- 20% от общего количества случаев — сбой в работе из-за отказа оборудования;
- 80% от общего количества случаев — сбой из-за неправильной эксплуатации оборудования клиентом.
Причина №1. Оборудование
Когда сбой касается непосредственно оборудования, в большинстве случаев достаточно установить причину происходящего — и устранение проблемы становится понятной и выполнимой задачей. Проанализировав характер ситуации, можно выявить закономерности, что поможет избежать повторения сбоев на схожем оборудовании или в аналогичной ситуации.
Пример
На автоматическом стеллажном штабелере произошел сбой: при движении боковой ролик ходового механизма задевал шину заземления. Ремонт, и соответственно, простой заняли 3 часа. Причиной стал открутившийся от вибрации крепежный болт. После повторного инцидента на другом стеллажном штабелере в регламентное ТО ввели пункт о проверке фиксации крепежного болта. Проблема больше не возникала.
Пример
На одном из участков конвейера каждый день происходил сбой: из 2000 тыс. коробов в среднем 10 застревали. Устранение проблемы не вызывало трудностей — требовалось выровнять короб, но это занимало примерно 5 минут. Казалось бы, ничего страшного, но суммарное время простоя конвейера составляло до 50 минут, в неделю — более 4-х часов, а в месяц — 2,5 дня, что уже немало.
Необходимо было выявить причину застревания коробов. Выяснилось, что на складской линии был участок, где короба перемещались с ленточного конвейера на роликовый под углом 90°. Роликовый конвейер включался при срабатывании установленного фотодатчика. Тяжелые короба проходили это участок, а вот легким не хватало кинетической энергии для перемещения к ограничительной планке и их разворачивало. Отрегулировав фотодатчик (сместив его назад на 1 см), проблему застревания коробов удалось решить.
Уменьшить время простоя оборудования можно и за счет сокращения периодичности работ во время регламентного технического обслуживания. Как показывает практика, нет необходимости выполнять некоторые регламентные работы с регулярностью, указываемой производителем. Предиктивный анализ и грамотная оценка специалистами текущего состояния оборудования дает возможность избегать замены еще годных деталей, а также позволяет спрогнозировать будущие ремонты заранее. В конечном счете это минимизирует расходы.
Пример
Для того чтобы снизить износ деталей и сократить частоту замены запчастей а, соответственно, время простоев, была произведена корректировка параметров частотного преобразователя на некоторых узлах. Ускорение, замедление, толчок и рывок при работе стали более плавными. Немного увеличился цикл выгрузки и загрузки, но это компенсировалось за счет сокращения простоя оборудования.
Причина №2. Человеческий фактор
Если же сбой произошел из-за неправильной эксплуатации оборудования, то установить причину может быть непросто. Чаще всего неприятности происходят из-за желания сэкономить. Но, как известно, «скупой платит дважды». Автоматизация склада — это зачастую дорогостоящий проект, требующий не только больших вложений, но и серьезного подхода. Чтобы все системы работали так, как ожидается, необходимо соблюдать рекомендации и использовать качественные материалы. Желание сэкономить на мелочах может привести к серьезным проблемам, сбоям в работе, а также вызвать неожиданные дополнительные траты.
Пример
Клиент использовал некачественные паллеты. Загруженные паллеты прогибались под тяжестью веса, из-за чего выгрузка со склада в автоматическом режиме была невозможна, а вручную этот процесс занимал много времени.
Пример
Клиент использовал некачественные коробки. При перемещении роботом-манипулятором у коробок регулярно открывалось дно, и весь материал разлетался в радиусе 3 м. На сборку и переупаковку уходило много времени.
Другой частой проблемой становятся халатность, некорректная работа персонала, отсутствие его необходимой квалификации из-за «текучки», а также несоблюдение необходимого регламента при работе.
Пример
В процессе работы складской системы был этап сканирования коробок. Некоторые штрихкоды были испорчены, и их нужно было сканировать вручную и потом вручную же изменить статус задания на «завершено» для WMS-системы. Иногда операторы этого не делали, из-за чего незавершенные задания накапливались, и выгрузка останавливалась. Чтобы изменить статус на завершенный, требовалось привлекать службу поддержи, на что уходило много времени.
Сократить время устранения отказа удалось путем сознательного мониторинга незавершенных заказов и принудительного их завершения в конце каждой недели. Для этого в WMS-системе потребовалось добавить дополнительное диалоговое окно.
Бесперебойное, отлаженное функционирование складских систем — это результат командной работы как обслуживающей организации, так и самого клиента. И желательно, чтобы в таком результате был заинтересован весь коллектив, от директора до рабочего.
Анализируя работу системы на конкретном объекте и используя опыт команды сопровождения, можно минимизировать простои оборудования, снизить риски выхода его из строя, а также избежать лишних затрат из-за простоев и сбоев в работе склада.
Интересное:
Новости отрасли:
Все новости:
Публикация компании
Достижения
Профиль
Контакты
Социальные сети