Как снизить производственные издержки при помощи нейросетей на 20%
Right line делится успешным опытом: внедрение нейросетей помогло промышленному холдингу сократить издержки на 20%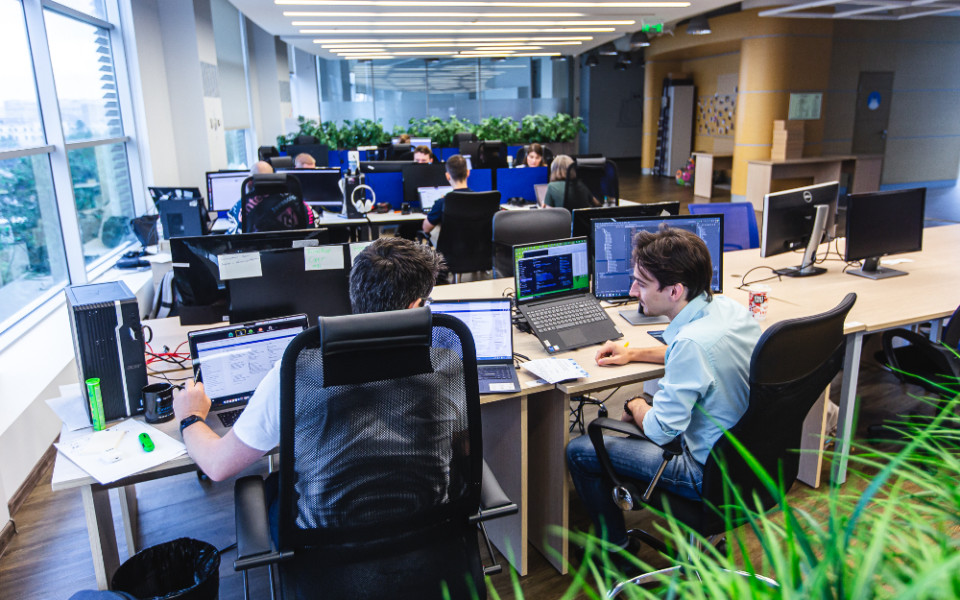
Задача
Крупный промышленный холдинг, специализирующийся на производстве металлических изделий, обратился в компанию Right line с запросом на предоставление инженеров по нейросетям. Заказчик хотел внедрить нейросеть в процесс отслеживания расхода материалов для производства, но столкнулся с необходимостью оптимизации модели и ее интеграции в существующие производственные системы.
Основная цель проекта заключалась в автоматизации процессов учета и контроля расхода материалов, чтобы снизить издержки и повысить эффективность производства.
Причины обращения
- Заказчик не обладал внутренними ресурсами для оптимизации нейросети и ее интеграции в производственные процессы;
- Проект требовал оперативного подбора специалистов с высокой квалификацией, чтобы избежать задержек в реализации;
- Холдинг стремился снизить издержки на производство за счет более точного прогнозирования и контроля использования материалов;
- Заказчик нуждался в увеличении скорости производства и уменьшении времени на ручные операции, а также хотел избежать возможных ошибок, связанных с человеческим фактором.
Шаг 1. Анализ потребностей заказчика
На данном этапе мы провели комплексный анализ текущих бизнес-процессов заказчика, чтобы понять специфику его работы и выявить ключевые боли. Для этого мы собрали и проанализировали данные о расходе материалов, включая показатели за предыдущие несколько лет, типы используемых ресурсов и объемы производства. Это позволило нам выявить основные проблемы: неточности в прогнозировании, избыточный расход материалов и периодические ошибки при ручном вводе данных.
В ходе анализа мы определили ключевые процессы, где использование нейросетей могло принести наибольшую пользу — прогнозирование расхода материалов на основе данных о предыдущих партиях продукции, автоматизация сбора и обработки данных с производственного оборудования, а также интеграция модели в существующие ERP-системы для минимизации ручного труда. На основе анализа мы составили четкое техническое задание: внедрение модели машинного обучения, которая могла бы точно прогнозировать расход материалов, учитывать особенности производственных процессов и легко интегрироваться в текущие системы холдинга.
Также мы разработали поэтапный план работ, включающий подбор специалистов, оптимизацию модели, ее интеграцию и тестирование системы. Это позволило партнеру заранее понимать сроки и этапы проекта.
Шаг 2. Подбор квалифицированных инженеров
Для реализации проекта мы привлекли команду ML-инженеров через наше направление Right team, которое специализируется на предоставлении услуг по заказной разработке и подбору высококвалифицированных IT-специалистов. Благодаря накопленному опыту и экспертизе, мы смогли за 2 недели найти и предоставить команду опытных ML-инженеров, обладающих необходимыми компетенциями для решения поставленной задачи.
Сначала мы определили ключевые компетенции, которые были необходимы для успешного выполнения проекта: опыт работы с моделями машинного обучения для прогнозирования данных, знание инструментов интеграции ML-моделей в производственные системы, навыки работы с большими объемами данных и их предобработки, а также понимание особенностей промышленных процессов и ERP-систем.
Затем мы использовали нашу собственную базу специалистов и провели активный поиск на профессиональных платформах. Было отобрано несколько десятков кандидатов, соответствующих всем требованиям заказчика. Каждый кандидат прошел отбор в несколько этапов, включая:
- техническое интервью для оценки уровня экспертизы;
- тестовое задание, имитирующее реальные задачи проекта;
- проверку soft skills для обеспечения слаженной работы в команде.
В итоге мы сформировали команду из опытных ML-инженеров, которые приступили к работе над проектом и в течение 5 месяцев успешно решали задачи по оптимизации нейросети и ее интеграции в производственные системы.
Шаг 3. Оптимизация и интеграция нейросети в производственные процессы
ML-инженеры начали работу с анализа существующей модели. Они выявили слабые места, такие как неточности в прогнозировании и избыточная сложность архитектуры, и предложили решения для их устранения. Модель была перестроена с учетом особенностей производственных данных заказчика.
На следующем этапе команда инженеров интегрировала оптимизированную нейросеть в производственные системы холдинга. Это позволило автоматизировать процесс отслеживания расхода материалов и исключить ручной ввод данных.
После интеграции система прошла тестирование в несколько этапов, чтобы убедиться в ее надежности и точности. На этом этапе были устранены все выявленные ошибки, и работа нейросети была доведена до максимальной эффективности.
Благодаря слаженной работе ML-инженеров, удалось на 20% снизить издержки производства. Также были автоматизированы процессы отслеживания расхода материалов, что позволило холдингу значительно сократить потери и оптимизировать использование ресурсов. За счет уменьшения времени на ручные операции и минимизации всех возможных ошибок также на 25% увеличился рост скорости производства.
Новая модель машинного обучения показала высокую точность в прогнозировании расхода материалов, что позволило лучше планировать производственные процессы. Внедрение нейросетей также позволило сотрудникам холдинга сосредоточиться на других стратегически важных задачах, освободив их от рутинных задач.
Интересное:
Новости отрасли:
Все новости:
Публикация компании
Профиль
Социальные сети