Первым делом самолеты: как избежать ошибки проектирования
Обзор международного опыта и инноваций в проектировании самолетов: какие прорывные технологии внесли весомый вклад и что поможет избежать ошибки проектирования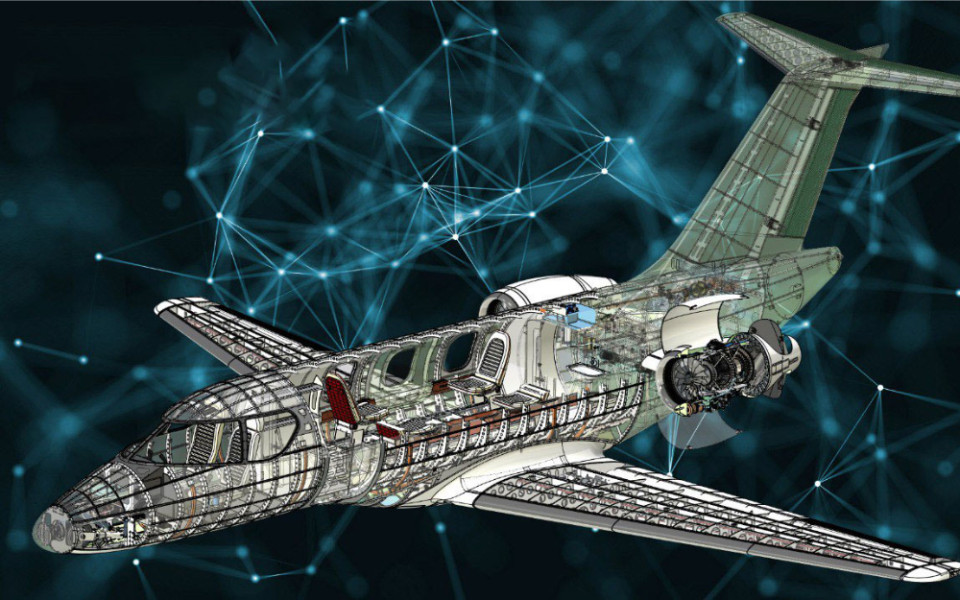
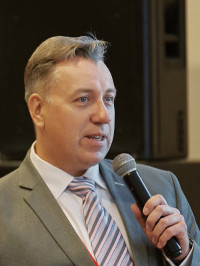
Эксперт по разработке архитектуры предприятия для внедрения ИТ и средств автоматизации, 30 лет опыта работы с производственными компаниями различного масштаба в разных отраслях промышленности.
Богдан, история «Boieng» неоднократно освещалась ведущими мировыми СМИ. Ваше мнение, как эксперта компании, которая создает инженерное ПО и работает с авиационным сегментом промышленности, действительно ли причина в ошибке проектирования?
Давайте попробуем разобраться. У всего всегда есть причина и следствие. Предлагаю рассмотреть предпосылки, чтобы понять происходящее. Вернемся на несколько лет назад и вспомним ситуацию и тенденции того времени: мир без границ, все сотрудничают со всеми, идет огромная волна глобализации. Все это способствует мобильности людей и авиакомпании создают давление на рынке — эффективность перевозки пассажиров должна расти, а значит, от производителей пассажирских самолетов требуют создавать более экономичные и более вместительные самолеты. Индустрия была на подъеме. Boeing в 2018 году, согласно официальным данным производителя, выпускает рекордное количество коммерческих самолетов — 806 единиц и темп идет по нарастающей. Для удовлетворения новых требований авиакомпаний делается модернизация существующих типов самолетов. Разработка нового типа самолета требует много времени и средств, поэтому модернизируются уже существующие типы. Но, главное — всему есть предел: конструкции современных существующих самолетов уже достаточно сильно оптимизированы, изделия стали очень сложными и вносить серьезные изменения становится все труднее. На фоне растущих требований и ожиданий в конструкцию воздушного судна были внесены изменения, потребность скорее вывести продукцию на рынок повлияла на процессы проверки внесенных изменений. Фактор времени сделал свое дело — пропустили недочеты. Эффект масштаба многократно усилил воздействие.
При разработке и выводе продукции на рынок очень важно принимать во внимание правило: цена ошибки, выявленной на этапе вывода и эксплуатации продукта, может стоить компании в сотни раз больше стоимости устранения самой ошибки, не считая издержек потери репутации, которые не поддаются прямому расчету. Как раз о важности своевременного выявления ошибок и коллизий, о возможности избежать их еще на этапе проектирования с помощью применения MBSE подходов, ранее рассказывал мой коллега — Игорь Кочан. Вернусь к теме: далее все переросло в идеальный шторм. Пандемия приостановила перелеты, снизилось взаимодействие между компаниями из разных стран, начали рваться коммерческие цепочки. Продажи самолетов существенно сократились уже как внешний фактор рынка.
То, о чем говорят СМИ сейчас, это результат событий последних пяти-шести лет и единовременное стечение различных обстоятельств. Большинство СМИ сфокусировались на результатах проблем компании «Boeing», а мне хотелось бы встать на сторону инженеров компании и акцентировать внимание на том, что компания сделала для развития всемирной авиации с точки зрения разработки изделия и как не допустить ошибок, которые могут отражаться на людях и компании-производителях в целом.
Давайте рассмотрим современные технологии в проектировании самолетов и развитии авиационной отрасли.
Одно из значимых событий, повлиявших не только на авиацию, но и на другие отрасли промышленности — это решение Boeing в 1989 году создать проект самолета семейства 777 полностью в электронном виде. В 1995 году впервые был собран полностью виртуальный двойник самолета, который сегодня называем электронный макет изделия (ЭМИ). Эффект был ошеломляющий. Во-первых, именно в электронном виде были идентифицированы несколько сотен различного рода геометрических коллизий, в основном электропроводных и трубопроводных магистралей и соединений. Во-вторых, высокая точность электронного макета позволила достичь такого результата, что уже первый экземпляр самолета не нуждался в доработке с применением дорогостоящего физического макета самолета. Теперь, для современной промышленности управление единым ЭМИ является основополагающей инженерной практикой.
Развитием темы использования виртуального изделия стало добавление элементов управления конфигурацией, в результате чего появилась возможность параллельно разрабатывать множество вариантов продукта на ранних стадиях развития программы. Сложность данного этапа обусловлена тем, что при небольшом объеме зафиксированных решений идет большое количество изменений. Подобный подход обеспечивает инженерному персоналу большую гибкость принятия решений, но при этом результаты всех действий очень точно применяются в определенных местах состава изделия для выборочного числа или всех экземпляров всего семейства.
Очень большой сдвиг в процессах и методах связан с реализацией новой программы «самолета мечты» семейства 787. В рамках программы были существенно пересмотрены подходы к проектированию и производству, конструкция систем и архитектура продукта в целом. В продукт были заложены новые требования, повышающие стандарты комфортного перелета для пассажиров, что повлияло на технологии и методы разработки. Так, самолет превратился в мехатронную систему, которая разрабатывалась с использованием методов системной инженерии. Впервые отработанная в проекте 777 система дистанционного управления «fly-by-wire» заменила механическую систему на синхронно работающий набор электрики, электроники, программного кода и механических исполнительных устройств. Новые возможности и ограничения принесло широкое использование элементов из композиционных материалов.
Отдельного внимания заслуживает организация процессов управления программой, управления цепочками поставщиков — соразработчиков, подготовки и управления производством. Целью было существенное сокращение (на 30-35%) времени цикла и стоимости разработки самолета. Была внедрена практика работы со стратегическими партнерами на условиях разделения рисков программы (поставщики, которые отвечали за предварительную сборку и поставку целых полностью собранных секций самолета). Общая доля компонентов, предоставленных поставщиками достигла 70% (рост в 2,3 раза). По сути, самолет начали выпускать конвейерным способом. Для прямого чтения актуальных данных стали использовать электронные мастер модели, в цехах вместо распечаток чертежей начали применять терминалы с доступом к информационным системам. Финальная сборка самолета теперь исчисляется в днях, а не месяцах. Естественно, все это было бы невозможно без глубокой модернизации процессов компании, разработки новых методов и адаптации средств автоматизации проектирования и подготовки производства.
Подводя итог, стоит отметить, что несмотря на все проблемы, Boeing остается сильным игроком с мощным научно-техническим и организационным потенциалом, а также, «законодателем моды» в процессе разработки коммерческих авиалайнеров. Многие из «ноу-хау» стали уже апробированными методами, в том числе перечисленные выше, и их описание уже давно публично доступно. Понимание и практическое применение этих отраслевых процессов и методов обеспечивает базу для разработки отечественных решений и технологий. Мы, в компании «Топ Системы» пристально следим за тем, как работают заказчики в различных индустриях, какие процессы и методы они используют. Результатом этой работы становятся адаптированные продукты и решения, которые мы предоставляем своим заказчикам. Таким образом, компания «Топ Системы» использует индустриальный подход. Набор устоявшихся процессов помогает заказчикам быстро адаптировать и внедрять их на своих предприятиях, а четкое следование этим процессам позволит избежать досадных ошибок и их тяжелых последствий.
Так чему же все-таки учит нас опыт «Boeing»?
В статье про труд инженера упоминалась закономерность: оптимизация разработки изделия во время проектирования влечет за собой влияние на затраты, которые невозможно снизить, не внося изменений в саму конструкцию изделия, и, дальше — вниз по цепочке производства. Поэтому надо помимо использования передовых средств проектирования и управления жизненным циклом изделия, современных информационных технологий, например, таких как, цифровые двойники, требуется осознанное применения технологий и комплексный подход, охватывающий выстраивание процессов компании и развитие персонала. Да, современные средства инженерных расчетов позволяют делать поверочный и точный расчет на виртуальной модели, выявлять коллизии, обеспечивают ускорение процесса валидации изделия при существенном снижении риска брака в физическом изделии, а возможность выполнить тестирование в виртуальном пространстве снижает потребность создания физических прототипов, а значит, позволяет сократить издержки на выпуск конечного изделия и повысить экономические показатели предприятия. Но, повышение скорости разработки не должно происходить в ущерб качеству — все технические риски должны быть тщательно исследованы, а экономические показатели могут быть существенным, но не единственным и главным критерием.
Интересное:
Новости отрасли:
Все новости:
Публикация компании
Профиль
Социальные сети