Статья расходов, о которой директора компаний почти ничего не знают
Есть такие расходы, которые зачастую вовсе не кажутся руководителям производств расходами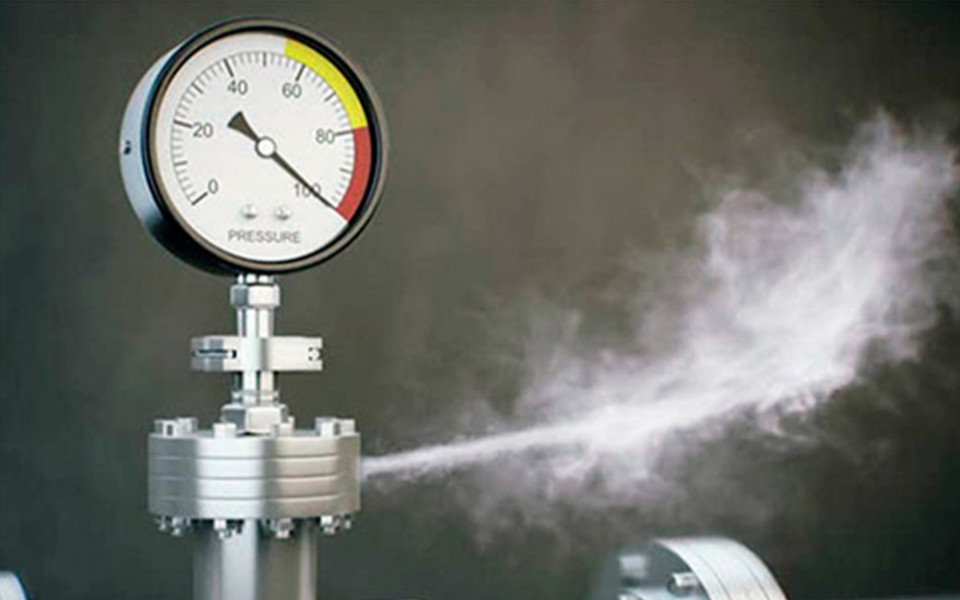
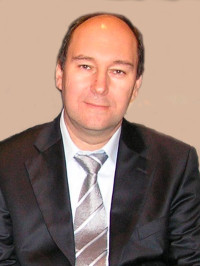
Многолетний опыт руководства службой сервиса у крупнейшего мирового производителя промышленного компрессорного оборудования. Самые сложные установки, техническое обслуживание и ремонт компрессоров.
Есть такие расходы, которые зачастую вовсе не кажутся руководителям производств расходами (либо существенными), всего лишь стоимость работы оборудования, его обслуживание и затраты на электроэнергию.
Однако, если посмотреть на это с точки зрения реальных цифр, то вот что получается: оборудование для производства сжатого воздуха — промышленный компрессор, одно из самых энергозатратных. Затраты на электроэнергию составляют примерно 80% всех затрат на эксплуатацию компрессорного оборудования.
Возьмем предприятие, на котором функционируют 10-15 компрессоров, где каждый выдает объем воздуха 10-12 куб./м. Воздух используется везде — от перемещения продукции до включения пневматического оборудования, пневмонасосов и других линий. На одном заводе с легкостью может функционировать до 1500 пневматических устройств.
Итак, сколько же сжатого воздуха «утекает в атмосферу» на таких производствах?
Мест, откуда «уходит» воздух предостаточно: трубопроводные соединения, конденсатоотводчики, негерметичные регуляторы, отверстия в проржавевших трубах и уплотнениях клапанов, не полностью закрытые вентили.
Ситуации случаются разные, например, необходимо ежедневно выполнять слив воды из конденсатоотводчика, оператор открывает вентиль, воздух с водой выходит в атмосферу пока она не закончится.
Но! Оператор может просто забыть закрыть кран позже или закроет его не до конца (возможное попадание грязи под уплотнение крана), так как воздушная утечка практически не различима на слух, особенно в условиях работы оборудования на заводе.
В своей практике приходилось побывать на большом количестве предприятий, работающих в разных отраслях промышленности. Нередки были ситуации, когда компрессор продолжал работать даже во время обеденного перерыва. Из-за утечек на оборудовании автоматика компрессора не могла дать команду на его остановку. А это не один кВт потребленной электроэнергии в день, не считая амортизационных расходов на компрессор, который не выключался! Простой расчет показывает потери только 10% сжатого воздуха из-за утечек: из 8 000 часов работы компрессора в год 800 часов он работал зря, зная потребляемую мощность легко вычислить сколько кВт электроэнергии, а также и денег улетело на ветер.
А если это крупный, например, нефтеперерабатывающий завод, где и компрессоров намного больше, потребляемая мощность выше, и трубопроводы доставки воздуха представляют собой огромные магистрали, то и объем утечек, естественно, выше.
В России считается, что в «норме» около 10% «утечки». Но в основном это гораздо более высокие показатели. Предприятие может сократить этот уровень до 5-8% с помощью программы распознавания и восполнения сжатого воздуха.
Для обнаружения утечек и снижения уровня теряемого сжатого воздуха проводится обследование и создание маршрута прохода воздуха — пневмоаудит.
В процессе используются ультразвуковые течеискатели, которые реагируют на звук воздуха, не уловимый для человеческого уха.
Самому предприятию не всегда легко справиться своими силами в поисках утечек, особенно, если это крупное производство.
Кроме того, нужно понимать, что слушать в условиях повышенного шума.
Ультразвуковой детектор не различает утечку воздуха и утечку пара. Он также собирает одновременно звук сжатого воздуха, пара или сжатого газа. Поэтому при определении утечки воздуха требуется сочетание знаний и методов определения.
Многие знают, что утечку можно замерить по уровню децибел, и это так, но только не на нефтеперерабатывающем предприятии потому, что вы ошибетесь с расчетами при постоянном фоновом шуме.
После выполнения пневмоаудита, предприятию предоставляется отчет обо всех обнаруженных утечках, места утечек помечаются табличками. В отчете рассчитывается общий объем потерь сжатого воздуха через утечки, а также его стоимость за год в денежном выражении. Все это позволяет предприятию сократить затраты за счет, казалось бы, незначительных потерь воздуха, а заодно и проверить состояние трубопроводов. Выгода и предприятию, и окружающей среде.
Некоторое время назад мы задались вопросом, как часто производственные предприятия проводят пневмоаудит, и провели исследование. К сожалению, получили печальные данные — только 14% из 200 опрошенных организаций проводили пневмоаудит когда-либо.
И мы больше, чем уверены в том, что пневмоаудит не проводят не потому, что жалко денег, а в большей степени потому, что просто не знают или, как говорится, «даже в голову не приходит», что это реальный работающий способ снижения затрат на производство продукции и амортизационные расходы на оборудование.
Интересное:
Новости отрасли:
Все новости:
Публикация компании
Достижения
Профиль
Контакты
Социальные сети